This is a first introduction to chiptuning for the 2.2L z22se ecotec engine in
the Opel Speedster and Vauxhall vx220. How a engine management worksThere are lots of stories about “chiptuning”, lots of different claims about
power, torque, driveability etc. Based on all the experience I’ve got with the
engine management on the 2.2L engine in the Opel Speedster I wrote this article
on how this engine management works. The engine management is nothing else then a computer with lots of connections.
Just like a PC it can’t do anything without software. On a PC commonly software
like Windows or Linux (the operating system) is used combined with different
applications. An engine management doesn’t need to have such broad features
as a PC. Almost all functionality that is available in a PC is redundant for an
engine management. But the basic idea remains the same. The engine management
has an operating system, just like a PC. But it is not written to be used with
all kinds of different applications. There are different software modules though
which can be added, depending on the kind of car the engine management is in
(for example ABS, ESP, cruise control etc.). The engine managements software is not stored on a hard disk like with a PC, but
is stored on a chip. Often it is possible to install a new version of the software
on this chip (for example to fix bugs). This isn’t as easy as with a PC, it usually
requires some dedicated equipment, often available only at dealers. [ecu.nl.jpg hoofdbrandstoftabel.png hoofdbrandstoftabel.thumb.png lft-en.png lft-en.thumb.png lft-tabel.png lft-tabel.thumb.png lft.png lft.thumb.png manifold.nl.jpg openloop-en.png openloop-en.thumb.png openloop.png openloop.thumb.png sft-en.png sft-en.thumb.png sft.png sft.thumb.png targetafr.nl.jpg]
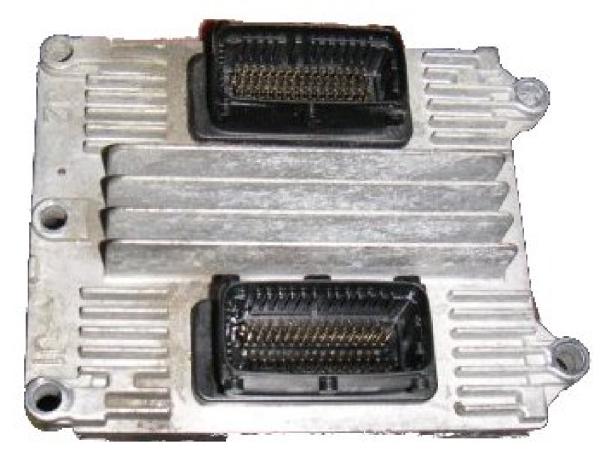 The way the software in the engine management works can be the same for a range
of different engines, for example a 1.6, 1.8 and 2.0. But the way the engine
management needs to control these engine is of course different. To prevent
each engine of having a specific version of the software, the specific values
for the different engines are stored in tables. This tables for example have
information on the amount of fuel the engine management needs to add depending
on the engine RPM and the throttle position. The content of these tables differ
from engine to engine, as the amount of fuel needed to keep a 1.6 engine
running is different from a 2.0. Changing these tables is a lot easier and
safer then having to make different versions of the software. And this is
exactly what chiptuners do, they change the values in these tables. A different
term for table is of course map, hence the term remapping. What happens during chiptuningThe goal with chiptuning is often to get more power from the engine. To be able
to get more power from an engine, you need to add something which can provide
this power. With a combustion engine this is fuel, in case of the 2.2L engine,
gasoline. To be able to burn the gas, oxygen is needed which is contained in
the air. To be able to get the most powerful combustion an engine needs a
specific ratio of air and fuel. So just adding more fuel will not help, more
air needs to be added too. With a turbo engine this is a relatively easy job
for the tuner. On modern turbo engine the engine management controls the turbo
pressure. By raising the turbo pressure, the amount of air is increased. By
adding more fuel, more energy is released during combustion and the engine
delivers more power. This explains the difference in claimed power increases
between normal (atmospheric) and turbo engines. But even with an engine like the 2.2L, it is possible to get more power by
making sure that the engine is effectively running the best air fuel ratio
to provide maximum power. The engine maker usually is on the safe side with
the air fuel ratio because of the world wide different conditions the engine
has to perform in. By further optimising the air fuel ratio some power can
be gained. What happens when changing the engineAn example of a popular change for the 2.2L engine is to change the intake
manifold for a better one. The standard intake manifold is a restriction for this
engine, it does not deliver enough air. By changing the intake manifold the
engine will be able to suck in more air, thereby adding more fuel and delivering
more power. [ecu.nl.jpg hoofdbrandstoftabel.png hoofdbrandstoftabel.thumb.png lft-en.png lft-en.thumb.png lft-tabel.png lft-tabel.thumb.png lft.png lft.thumb.png manifold.nl.jpg openloop-en.png openloop-en.thumb.png openloop.png openloop.thumb.png sft-en.png sft-en.thumb.png sft.png sft.thumb.png targetafr.nl.jpg]
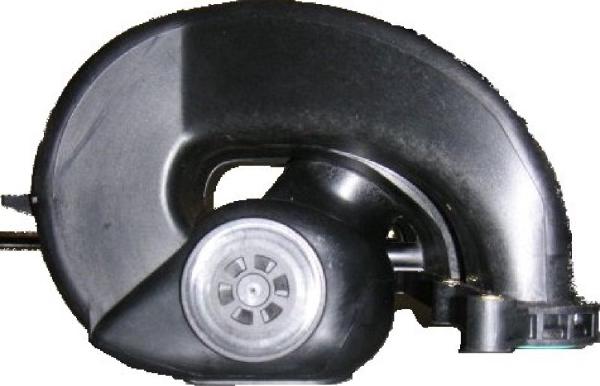 But there are different results when placing a different intake manifold (discarding
the difference in intake manifolds being used). This can be explained by the way
the engine management works. Making the mixtureLets assume 1 simple table in the engine management which contains the throttle
valve position on the y-axis and the engine RPM on the x-axis. Each cell in this
table contains a value. These values indicate the amount of fuel the engine
management needs to add for this specific combination of throttle and RPM. [ecu.nl.jpg hoofdbrandstoftabel.png hoofdbrandstoftabel.thumb.png lft-en.png lft-en.thumb.png lft-tabel.png lft-tabel.thumb.png lft.png lft.thumb.png manifold.nl.jpg openloop-en.png openloop-en.thumb.png openloop.png openloop.thumb.png sft-en.png sft-en.thumb.png sft.png sft.thumb.png targetafr.nl.jpg]
 After changing the intake manifold, the same throttle position will allow in a
different amount of air. So if the same amount if fuel is still used, the air
to fuel ratio will not be correct anymore. The least this will impair the engine
performance, but in extreme cases it can damage the eninge. There are of course more subtle situations where the amount of oxygen entering
the engine for a specific throttle position is different. Think about changes
in the air temperature and pressure, but also engine wear. To be able to compensate
for these kind of situations a special mechanism is built into the engine
management. This mechanism uses an oxygen sensor (also known as a lambda sensor)
in the exhaust system. Through this sensor the engine management is able to
determine the amount of oxygen left in the exhaust gases. If the ratio between
air and fuel is optimal, the amount of oxygen left in the exhaust gases will
be minimal. For gasoline the optimal ratio between fuel and air is 1 to 14.7, so
there is exactly enough air for the amount of fuel, and the burn process is
complete. The sensor in the exhaust will indicate to the engine management if
the ratio was lower then 1:14.7 (too much fuel for the amount of air) or lower
then 1:14.7 (too little fuel for the amount of air). How much the ratio differs
from 1:14.7 can not be determined by the signal from this sensor. During operation of the engine, the engine management will continuously try
to get the lambda sensor as close to 1:14.7 as possible. The engine management
read the fuel value from the main fuel table, and checks the last reading
from the lambda sensor. If the signal indicates too little fuel, an extra
addition will be made and vice versa. This way the engine management continuously
tries to optimise the air to fuel ratio. These changes in the ratio are called
trims. As these trims are taking place quite quickly, they are known as
short term fuel trims (SFT). This changes take place in a loop like process,
which is known as closed loop operation. [ecu.nl.jpg hoofdbrandstoftabel.png hoofdbrandstoftabel.thumb.png lft-en.png lft-en.thumb.png lft-tabel.png lft-tabel.thumb.png lft.png lft.thumb.png manifold.nl.jpg openloop-en.png openloop-en.thumb.png openloop.png openloop.thumb.png sft-en.png sft-en.thumb.png sft.png sft.thumb.png targetafr.nl.jpg]
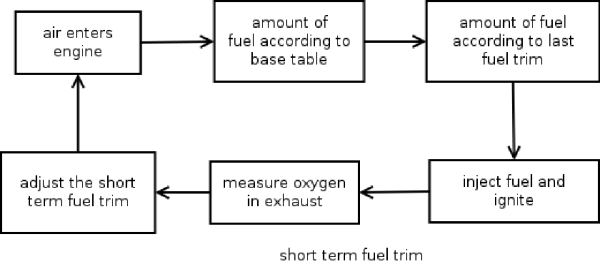 The process of trying to optimise the value from the base fuel table is
not optimal. The changes are reactive, the loop needs to be traversed a
couple of times to get the changes right, and this takes time. To save
time and have a better initial air to fuel ratio the engine management
creates a temporary table in memory. Depending on engine operating conditions
the engine management will fill this table with deviations on the base
fuel table. The advantage of this setup is that the amount of fuel will
now directly be corrected without having to look at the lambda sensor
first. This table contains fuel trims that are collected over a longer
period of time. Therefor it is called a long term fuel trim (LFT). [ecu.nl.jpg hoofdbrandstoftabel.png hoofdbrandstoftabel.thumb.png lft-en.png lft-en.thumb.png lft-tabel.png lft-tabel.thumb.png lft.png lft.thumb.png manifold.nl.jpg openloop-en.png openloop-en.thumb.png openloop.png openloop.thumb.png sft-en.png sft-en.thumb.png sft.png sft.thumb.png targetafr.nl.jpg]
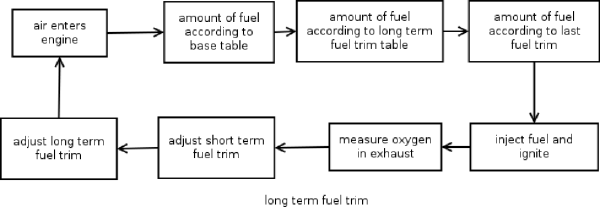 The engine management in our engine has a luxury LFT. It consists of
a table with multiple cells. This table isn’t as large as the base
fuel table. But there are also engine managements which work with
only 1 LFT value for all operating conditions. For a standard engine
this isn’t much of a problem. For variations in weather and engine
wear such a table adequate to compensate the changes in fueling. The
engines character is still the same, and this character is what is
embedded in the fueling information stored in the base fuel table. [ecu.nl.jpg hoofdbrandstoftabel.png hoofdbrandstoftabel.thumb.png lft-en.png lft-en.thumb.png lft-tabel.png lft-tabel.thumb.png lft.png lft.thumb.png manifold.nl.jpg openloop-en.png openloop-en.thumb.png openloop.png openloop.thumb.png sft-en.png sft-en.thumb.png sft.png sft.thumb.png targetafr.nl.jpg]
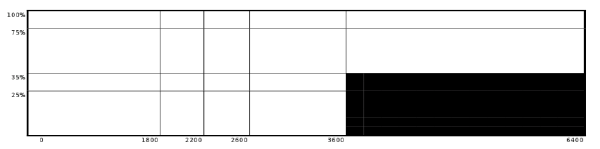 The difference with the base fuel table is pretty clear. The base fuel
table has over 350 cells. The LFT table only has 18 cells. Now the situation where the intake manifold is placed. This gives a significant
change in the character of the engine. The flow of the intake manifold
differs with RPM’s. The trim mechanism in the engine management will of course
still work, but due to the character change in the engine it is very difficult
to fit all these changes in the small LFT table. Especially the cells in the
LFT table that account for a large operating range of the engine will change
often, because one of those cells needs to compensate for a whole range of
different fuelings. Basically, the values in the LFT table are never correct. More powerTo get the engine to deliver maximum power a different fuel to air
ratio is needed then 1:14.7. More fuel needs to be added to make
maximum power. For the engine management this is quite straight forward.
The engine management has been programmed that on full throttle (so delivering
maximum power) it needs to deliver an air to fuel ratio of 12.6:1. Because
the engine management knows how to make an air to fuel ratio of 14.7:1 (through
the base fuel table and all the trims) it can calculate how much fuel
needs to be added to make a ratio of 12.6:1. This type of air to fuel ratio
is also know as a target air to fuel ratio or a target AFR. The word
target indicates that the engine management can’t be sure the AFR is
correct. The lambda sensor in the exhaust isn’t able to indicated the
engine management how far the air fuel ratio is below 14.7:1. So there
is no way for the engine management to verify. No loop is active anymore
to verify and control the exact air to fuel ratio, so this mode of
operation is also know as open loop. [ecu.nl.jpg hoofdbrandstoftabel.png hoofdbrandstoftabel.thumb.png lft-en.png lft-en.thumb.png lft-tabel.png lft-tabel.thumb.png lft.png lft.thumb.png manifold.nl.jpg openloop-en.png openloop-en.thumb.png openloop.png openloop.thumb.png sft-en.png sft-en.thumb.png sft.png sft.thumb.png targetafr.nl.jpg]
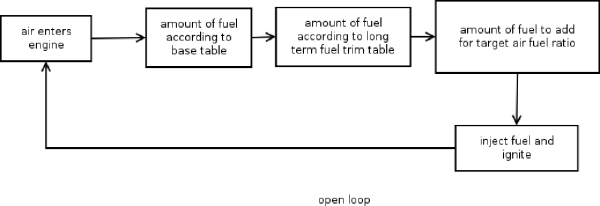 From the information above it is quite clear that it is very important
that the engine management accurately knows how to make a 14.7:1 air
fuel ratio. When changing the intake manifold, this will no longer be
the case. The LFT table contains a cell which covers almost half of
the RPM range on full throttle. The chance this cell contains the
correct value for this whole operating range is 0. Therefor the engine
management will not be able to make the required target AFR and so the
engine will not deliver full power. Below a power graph can be seen for an Opel Speedster. The lower graph is for
a target AFR of 12.7:1, the higher graph is for an AFR of 12.9:1. [ecu.nl.jpg hoofdbrandstoftabel.png hoofdbrandstoftabel.thumb.png lft-en.png lft-en.thumb.png lft-tabel.png lft-tabel.thumb.png lft.png lft.thumb.png manifold.nl.jpg openloop-en.png openloop-en.thumb.png openloop.png openloop.thumb.png sft-en.png sft-en.thumb.png sft.png sft.thumb.png targetafr.nl.jpg]
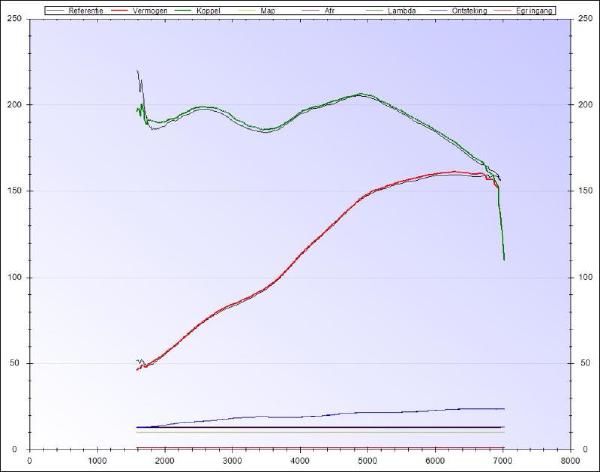 Such tiny changes in AFR give a reproducible change in engine performance and
signifies the importance of an accurate target AFR. ConclusionAn engine management has a compensation mechanism that is able to compensate
for weather influences and engine wear for an engine which has the same
character as the engine management was calibrated for. This compensation can
be done with a table which is much coarser then the base table. When changing the engine’s character, the LFT table is too coarse to compensate
for the character changes. The cells in the table are too large. This causes the engine to not operate optimally and in extreme cases can lead to
damage. The performance for the engine will not be optimal. Depending on the current
values in the LFT table, the performance can be different from measurement to measurement
and can be quite significant. The solution for this is to modify the base fuel table in the engine management so
each position in the table contains the correct amount of fuel for a 14.7:1 air to
fuel ratio. This way the engine management will be able to make the target AFR and
the engine will deliver optimal power. When optimally chiptuning an engine management it is not possible to optimize the
base fuel table on one engine and copy it to another engine. The base table is
dependant on the state of the engine, including all modifications and will be different
with different engine modifications. |